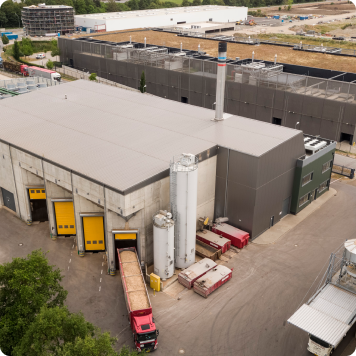
01
Green heat and electricity production
Read moreDiscover
Kiowatt was created in 2008 by LuxEnergie S.A. and its partner, Groupe François S.A., to strengthen their activities in the biomass sector.
The Kiowatt site at Roost/Bissen specialises in large-scale biomass trigeneration, i.e. the production and distribution of electricity, heat and cooling.
Moreover, it is the only wood pellet production site in Luxembourg.
01
Green heat and electricity production
Read more02
Production of BADGER Pellets®
Read more03
Green cold production
Read more01
The combined heat and power plant, which can simultaneously generate green heat and electricity from the same renewable energy source, is at the heart of the industrial site. Every year, it is fuelled by 42,000 tonnes of end-of-life wood from Luxembourg. The combustion heat is used to produce superheated steam in the boiler, which is then used by a turbine (2.8 MW) to generate green electricity and, at the same time, green heat.
At full capacity, the plant can generate 24 GWh of green electricity per year, which is then fed into the public grid. This amount is enough to supply some 6,600 households and replaces an equivalent amount of electricity that would otherwise have to be generated from fossil fuels.
This green electricity generation thus contributes to reducing our carbon footprint.
Most of the thermal energy produced in the boiler, i.e. around 108 GWh per year, is used for the following three applications:
Using this heat also makes it possible to replace energy that would otherwise have to be produced using fossil fuel and hence reduce CO2 emissions.
02
The pellet production plant uses only debarked fresh wood.
The raw material for the manufacture of wood pellets consists of sawdust, fresh wood chips as well as small-diameter logs, which cannot be manufactured into durable products and whose characteristics and variations we monitor. The final quality of our pellets depends on the quality of this raw material. Thanks to the stability and our analyses of the raw material, BADGER Pellets® are of consistent quality and guarantee the optimal operation of your stoves and boilers.
The logs are first debarked and then chipped and transferred to a wet chip and sawdust silo. The next stage of processing involves removing any ferrous metals from the material stream using a magnetic separator.
The sieved sawdust is transported to a low-temperature dryer, while the oversized shavings are sent to a shredder to be broken up. They are then screened again. In the low-temperature dryer (the energy required comes from the thermal heat produced by the cogeneration plant), the sawdust is spread over a wide belt through which heated air flows from top to bottom, and dried to a moisture content of around 7%. It is then transported to the silo. The dried sawdust is transported to the pellet presses, where the wood is subjected to high pressure as it passes through dies, and is transformed into wood pellets. The pellets produced are then cooled, sieved and stored in the pellet silo.
BADGER Pellets® are combustible wood pellets made from sawdust produced by sawing wood from our regions. The sawdust, without bark, is agglomerated in this form thanks to the combined action of high pressure and lignin, a natural constituent of wood which gives our pellets their shiny surface. With BADGER Pellets®, no glue or chemical additives are used. It is a 100% natural fuel!
Our BADGER Pellets® have several certifications which are important indicators:
BADGER Pellets® are high quality fuels, ENplus®A1 and DINplus certified. By controlling our raw material (completely debarked) and thanks to regular analyses and audits, we can guarantee the consistency of this quality and compliance with all the strictest criteria required by these certifications.
For DINplus certification, please consult the official website by following the search procedure with n°7A072.
With the recasting of the Directive on the promotion of the use of energy from renewable sources (Directive (EU) 2018/2001 – RED II), the share of bioenergy in meeting our energy needs will increase considerably in the future. In order to guarantee that the biomass used for this purpose has been produced in a sustainable manner, the European Member States have agreed on criteria that will in future have to be respected and documented by all economic players using biomass – or biogas – to produce electricity or heat. Voluntary certification schemes such as SURE are seen as an objective and reliable way of documenting compliance with these RED II criteria. To this end, the schemes are audited and recognised by the European Commission to ensure full compliance with RED II requirements and to guarantee high quality and transparency of sustainability certification.
The biomass from Kiowatt Pellets S.A. carries an SBP claim and is accompanied by verified energy and carbon data, from biomass producer to end-user allowing carbon emissions calculations to be made.
Kiowatt Pellets S.A. holds the PEFC label (Certificate number: WOODBE-PEFC-COC-001075), which certifies that the wood-based products come from sustainably managed forests. It ensures that forest management complies with strict environmental, social and economic criteria, thereby helping to conserve forests and protect the environment.
Since 2014, Kiowatt Pellets S.A. has been proud to bear the “made in Luxembourg” label, a registered trademark that certifies the Luxembourg origin of Luxembourg products and services. This label was created on the initiative of the Ministry of Foreign Affairs, the Chamber of Commerce and the Chamber of Trades.
We have an efficient distribution network in the Greater Region! The pellets are transferred from the silo to a filling plant, which is then used to load the blower lorries for bulk delivery.
To ensure a professional supply, BADGER Pellets® are distributed in Luxembourg by Husting & Reiser S.A.. This distributor has its own blower lorries (approved by metrology), to provide you with the best service and a high-quality product.
Husting & Reiser S.A.
13, rue d’Ell
L-8509 Redange / Attert
T : 23 62 10 75
03
On the same site there is a refrigeration plant from the company DataCenterEnergie S.A. (partnership of the companies LuxEnergie S.A. and LuxConnect S.A.). It produces cold for the LuxConnect S.A. data center, which is located just opposite the Kiowatt factory.
The technical concept of the DataCenterEnergie cold plant is based on the production of cold by means of absorption refrigeration machines which are powered, on the thermal side, by the exhaust steam from the Kiowatt wood recovery installation.
The two absorption chillers have a cooling capacity of 2,500 kW each. To achieve this result, they require a heat output of 3,550 kW per absorber.
The heat supply is provided via a district heating network between the Kiowatt heating plant and the DataCenterEnergie facility.